- The installation method of new wire rope and the specific process of putting into use.
- Operation skills and working habits of the operator.
- Self maintenance of the wire rope during its service life.
- Maintenance of the system itself during the operation of the wire rope
Operation suggestion
We have summarized a number of operational recommendations designed to help you extend the life of your wire rope. Each part of this paper expounds the methods of extending the effective service time of wire rope from different dimensions. That's why you need to know all about this article.
When installing the new wire rope, it is important to avoid twisting.
The wire rope needs to be properly unloaded from the I-wheel or reel and installed on your equipment. On a smooth drum, the first layer of wire rope must be tightly wound.
Properly activate the new wire rope
After the wire rope is installed, it should be run for a period of time without any load. Then, in order to obtain the best results, the load and speed of its operation should be controlled so that the strands and wires in the rope can adjust themselves.
Structural elongation
When initially put into use, in the process of positioning between strands and strands and between strands and rope core, the new wire rope usually extends, which is called "structural elongation". Given that this is an inherent structural characteristic of the wire rope, and the structural elongation of each wire rope is not the same. For standard wire ropes, the elongation is usually 0.25%-196 of the length of the rope. If structural elongation needs to be minimized, the wire rope needs to be pre-stretched before leaving the factory. Please give details when signing the order. Another type of elongation is elastic elongation, which is caused by the recoverable deformation of the metal itself.
End cutting and wear point elimination
If increasing wear is observed in local areas, a small section of the wire rope should be cut. This operation may require the initial length of the wire rope to be slightly longer than you are used to. Such as the tow rope of the traction rope or the retracting rope of the grab bucket, if there is serious wear near the tail end or any concentration area, or there is a large number of fatigue broken steel wire, these wear parts are removed, which can effectively extend the service life of the wire rope.
The steel wire at the end breaks due to vibration fatigue, so a small section of the steel wire rope at this part is cut and re-wedged, which is conducive to improving the service time of the steel wire rope. Once a fracture is detected, the section of the wire rope from the fracture to the fixture shall be cut, and the entire section of the wire rope covered by it shall be cut. In the alveolar area, at least 1.5 to 1.8 meters should be removed. Clips and fixtures should be cut until no broken wires exist.
At the balance guide wheel equipped with most overhead cranes, the area where the rope is in contact with the balance guide wheel is prone to fatigue. If you cut a small section of the wire rope at one end of the drum to stagger the contact point between the rope and the guide wheel, you can increase the service life of the rope. It is important to remove the balance guide before wear becomes severe and to remove it from the same drum.
Regular cleaning and lubrication to reduce wear
During the production process, we will perform lubrication operations on the wire rope, aiming to enable the strand and the steel wire within the strand to automatically adjust with the movement and bending of the wire rope. However, lubrication during the production process is difficult to ensure that the wire rope is adequately lubricated throughout its life cycle. Therefore, during the service life of the wire rope, regular lubrication operation is extremely critical.
During the operation process, the surface of the rope will be covered with dirt, stone chips or other materials. Such a situation will hinder the infiltration of the lubricating oil applied on the site into the steel wire rope, so it is necessary to clean the steel wire rope before the lubrication operation.
The lubricating oil used should have the characteristics of low consistency, only so that it can penetrate into the rope core. Generally speaking, there are three types of lubrication: drip, spray and hand brush. No matter which method is used, lubrication should be carried out at the bending part of the wire rope, such as the place of the groove wheel. We recommend that you apply lubricating oil to the top of the bend because the strand of the rope here stretches due to the bend and is easier to penetrate. In addition, pressure lubrication can also be used in the commercial field. The service life of the wire rope is directly related to the type of lubrication you use and the effectiveness of the amount of lubrication.
Proper lubrication should be able to effectively reduce friction, prevent corrosion, and adhere tightly to each wire. At the same time, it must have good flexibility, there should be no cracks or cracks in the low temperature environment, and there should be no dripping in the high temperature environment. It is strictly prohibited to apply excessive grease to the wire rope, because this will cause the wire rope and the attached hard object to rub against each other, and then damage the wire rope. Used machine oil should also not be used, as it contains substances that damage the wire rope. If the circumstances are exceptional, you have the right to instruct us to use special lubricants in the production process.
Inverted end
Areas with severe wear are often too far from the end, or the wear is too long to be removed. In this case, you can reverse the two ends of the rope and place the less worn part in the area that is prone to wear. This type of operation is useful for tilting and pulling ropes. The end inversion must be carried out before the wear level reaches the replacement standard. When the tail end is inverted, kinks should be avoided as much as possible to reduce the damage to the wire rope.
For example, in the transmission system of some large machinery, the lubrication of the wire rope and the tail end inversion operation are particularly critical. If the lubrication is not proper, it may lead to the operation of the whole system failure, resulting in huge economic losses. If the tail end inversion is not timely and improper operation, it will also affect the service life and safety of the equipment. For example, in the construction lifting equipment of high-rise buildings, a slight negligence in these handling of wire ropes may cause serious safety accidents.
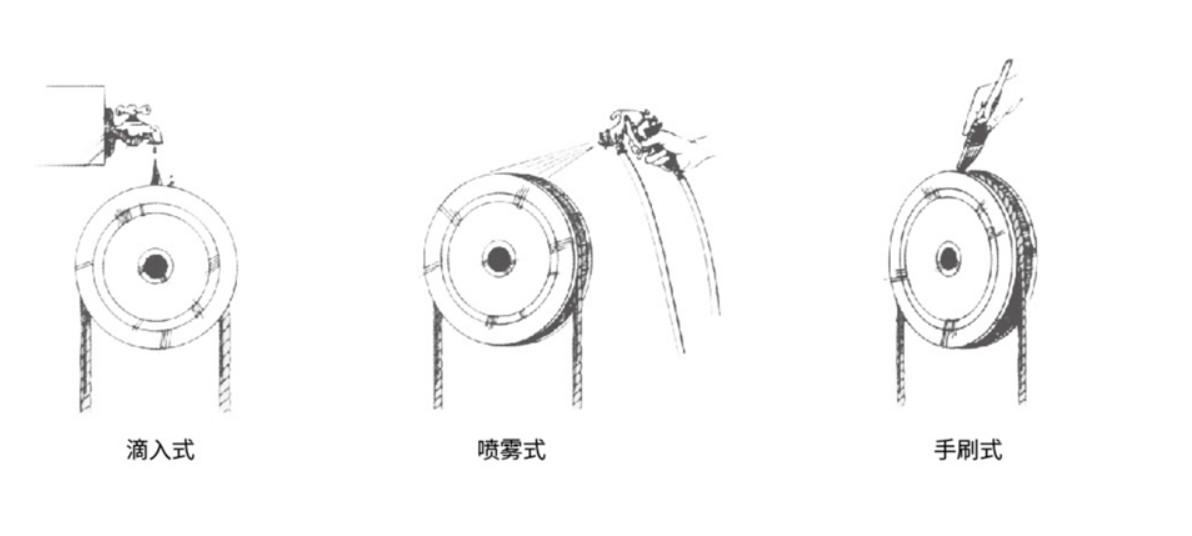